Essential Tools for Crafting Beautiful Rings
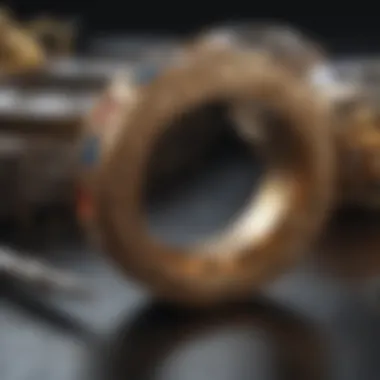
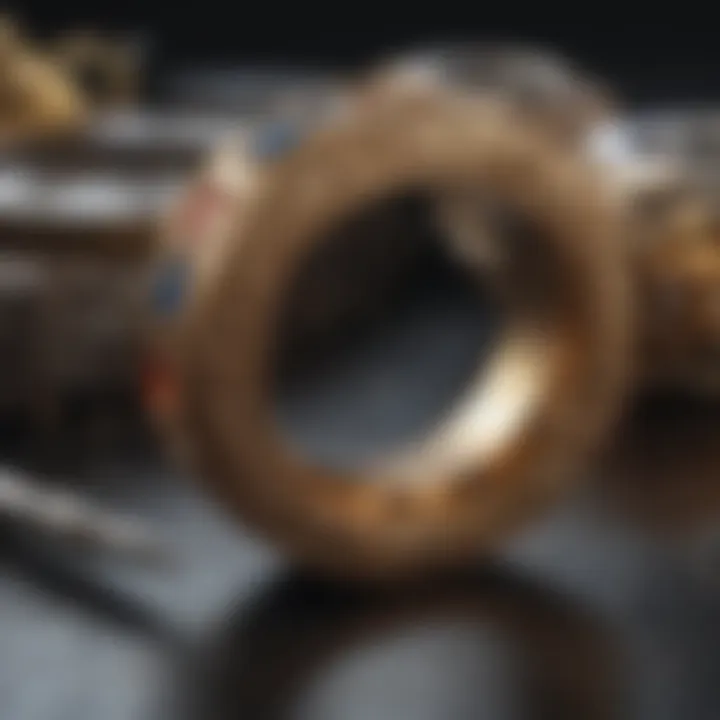
Intro
Ring making is a delightful art form that blends creativity, precision, and a touch of science. Even for those who think of it just as a hobby, there's much to learn about the tools and techniques that make stunning rings possible. This journey encompasses everything from the intricacies of gemstones to the various equipment that jewelers use. Whether you're picking it up casually or diving into it as a career, understanding these elements will enhance your craft through deeper insights and skills.
As we step into this exploration, we'll shine a light on the essential tools, their functionalities, and some insights into modern and traditional methods of ring making. Comparing the old with the new provides a fascinating context for understanding today’s technologies, while also paying homage to timeless practices that have informed jewelry making across cultures.
Gemstone Overview
Definition and Characteristics
Gemstones are not merely decorative pieces; they encompass unique characteristics that make them valuable in the world of jewelry. Each gemstone has attributes that speak to its natural beauty and rarity. For instance, diamonds are renowned for their hardness, while emeralds are celebrated for their vibrant green hue.
Some key characteristics include:
- Color: This can vary greatly, not just by type of gemstone but also within the same category, influenced by impurities and treatments.
- Clarity: Refers to the presence of internal flaws or inclusions, where a gemstone's clarity can determine its value.
- Cut: The manner in which a gemstone is shaped and polished has a significant impact on its sparkle.
- Carat Weight: The size of the gemstone, measured in carats, often plays a role in the price and appeal.
Classification of Gemstones
Gemstones can be classified primarily into two categories: precious and semiprecious. The classification often hinges on factors like rarity and desirability. Precious stones like rubies, sapphires, emeralds, and diamonds have a long-standing reputation, while semiprecious stones include amethyst, topaz, and aquamarine.
"Every gemstone tells a story, holding within it a history of its formation, the earth's creativity, and the craftsman's touch that transformed it into a piece of art."
In addition to that primary classification, gemstones can also be grouped based on their chemical composition, such as carbonates, oxides, and silicates. This classification is especially beneficial for jewelry designers and collectors as it can guide decisions on durability, suitability for certain pieces, and care needed for preservation.
Next, we shall dive into the historical significance of gemstones in jewelry making. The essential role they played in various cultures throughout time adds a layer of context that enriches any designer's work.
Understanding Ring Making Equipment
Understanding ring making equipment is not just a technical necessity; it's the backbone of creating exquisite jewelry. Without a firm grasp of these tools, both aspiring jewelers and seasoned professionals can find themselves at a standstill, unable to translate their creativity into tangible form.
When we dive into the world of ring making, we uncover a diverse array of tools and machines, each serving a distinct purpose. From the most basic pliers to advanced 3D printers, these instruments enable artisans to craft designs that can be as simple as a delicate band or as intricate as a gemstone-studded masterpiece.
While many might think of jewelry making as an art solely dependent on creativity and aesthetic vision, the importance of functionality and understanding the equipment cannot be overstated. The right tools not only enhance effectiveness but also improve precision and creativity in the design process. Familiarity with ring making equipment can lead to better outcomes, reducing trial and error in crafting.
Definition and Purpose
Ring making equipment encompasses a variety of tools and machinery that assist in the design, fabrication, and finishing of rings. This includes not just basic hand tools like hammers and saws but also more complex equipment like laser-cutting machines and soldering tools.
The primary purpose of these tools is to facilitate the transformation of raw materials—such as metal and gemstones—into finished jewelry pieces. However, each tool offers unique advantages:
- Precision: Tools like mandrels help in achieving accurate sizes and shapes.
- Efficiency: Machinery such as polishing machines can save time while enhancing quality.
- Creativity: Advanced tools allow for innovative designs that were previously difficult or impossible to create by hand.
To cap it off, knowing the definition and purpose of these tools lays the groundwork for a deeper exploration of ring making, as each piece of equipment contributes to the overall narrative in the jewelry-making process.
Historical Context
The evolution of ring making equipment mirrors the journey of human craftsmanship itself. Historically, jewelry was fashioned with rudimentary tools—stones, wood, and bones were common in ancient times. As cultures developed, so did the sophistication of their tools.
In Ancient Egypt, craftsmen used simple metalworking tools like hammers and pliers, which enabled them to create stunning gold jewelry. The introduction of new materials, such as iron and later, stainless steel, revolutionized jewelry production, allowing for greater durability and design complexity.
Fast forward to the Renaissance, where the artistry in jewelry saw remarkable advancements due to improved metalworking techniques and the introduction of soldering. In the modern era, we witness an explosion of technology entering the ring-making space. Laser cutting and computer-aided design (CAD) systems have become commonplace, leading to unprecedented levels of precision and customization.
Understanding this historical background provides insight into how tools have shaped jewelry design over millennia and how they continue to evolve in tandem with new technologies and ideas. This knowledge is critical for anyone looking to appreciate the artisan's craft or even dive into jewelry making themselves.
Essential Tools for Beginners
When diving into the world of ring making, having the right tools is not just helpful; it’s essential. Beginners may feel overwhelmed with the range of equipment available, but understanding the key tools can make all the difference between a smooth crafting journey and a frustrating experience. Each tool serves a distinct purpose that contributes to the creation of beautiful rings, and knowing what to use and when can elevate your craftsmanship significantly.
The importance of starting with a solid foundation of essential tools cannot be overstated. These tools not only simplify the process but also ensure that mistakes are minimized as you learn. Furthermore, they can foster creativity and experimentation, allowing new jewelers to explore their artistic inclinations without being bogged down by inefficiencies.
Basic Jewelry Making Kit
A jewelry making kit is typically the cornerstone of any beginner's venture into ring crafting. Such a kit often includes fundamental items like a variety of pliers, wire cutters, and other basic hand tools.
- What’s included? Some common components might feature:
- Round nose pliers for shaping wire
- Chain nose pliers to grip and bend a variety of materials
- Flat nose pliers for holding rings securely during work
While purchasing a pre-made kit can be convenient, consider your specific needs as they may differ based on the type of rings you want to make. It’s worth investing in quality tools from the get-go. Cheap options might save money short-term, but they often lead to inaccuracies and frustrations. A well-made basic kit will last for years, making it a worthy investment into your newfound skill.
Wire Cutters and Pliers
After the initial kit, wire cutters and pliers emerge as vital accomplices in your crafting saga. These tools allow for precise cutting, bending, and shaping of wires that form the backbone of many ring designs.
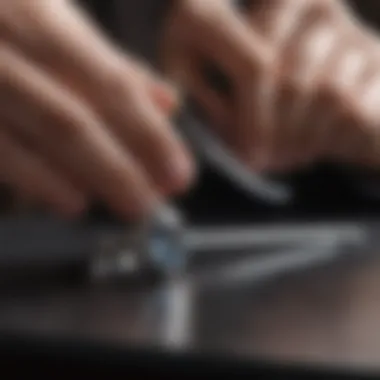

- Wire Cutters: These are specifically designed to slice through various gauge wires without fraying the ends. When selecting wire cutters, ensure they are rated for the types of metal you intend to use—soft metal versus harder metals will require different kinds of cutting action.
- Pliers: Different pliers serve various functions. For instance, round nose pliers help create loops in wire, which are essential for linking or attaching components. Conversely, chain nose pliers can help open or close jump rings and aid in shaping designs without leaving marks—essential for your polished final product.
Mandrels and Ring Sizes
Understanding ring sizes is paramount in creating well-fitted jewelry. Mandrels are indispensable in this aspect, serving as tools to size, shape, and even test your rings. You’ll find that a good mandrel will help you understand how the ring will fit without needing to repeatedly measure each piece.
- Mandrel: This tool, often made of metal or wood, is tapered and comes in various sizes to create rings of different dimensions. When you place a piece of wire or metal around the mandrel, you can stretch or hammer it into shape, ensuring it’s an accurate size before completing the piece.
- Sizing Charts: It can be useful to keep a ring size chart handy while you craft. This not only ensures that your pieces fit well but also improves your accuracy when making rings for others. Sizing is often considered the difference between an amateur and a professional finish.
In summary, getting started with the right set of tools lays a strong foundation for any aspiring ring maker. It’s like building a house—the sturdier your foundation, the more creative and elaborate your constructs can be. Understanding these essential tools and their specific roles can pave the way for a truly rewarding and expressive experience in ring making.
Intermediate Equipment Choices
As one moves beyond the basics in ring making, the equipment used can significantly enhance both the quality and efficiency of the work. Intermediate equipment choices serve as a bridge between simple hand tools and the advanced machinery used in professional settings. In this section, we’ll examine essential intermediate tools, and their important roles in the jewelry-making process. Beyond just the functions, we'll dig into how each tool can influence the final product and elevate a jeweler's craft.
Soldering Tools
Soldering tools play a critical part in the assembly of rings, especially as designs become more intricate. This process involves melting a filler metal, known as solder, to join two metal pieces together. The variety of soldering tools ranges from handheld torches to soldering stations. Each has its own merits depending on the complexity of the project and the materials used.
A useful soldering tip is to always ensure that the surfaces to be joined are clean and well-prepared, as this significantly impacts the strength of the bond. Here are a few key soldering tools:
- Butane Torch: Ideal for small jobs, it provides precise heat control.
- Soldering Iron: Optimal for delicate work where a more steady hand is needed.
- Flux: This helps clean the metal surfaces, preventing oxidation during the soldering process.
Mastering soldering techniques can take some time, but the results yield far more durable and professional-looking pieces. Plus, the ability to solder enables jewelers to experiment with more advanced designs that would be difficult or impossible otherwise.
Polishing Machines
A well-polished ring can make all the difference when it comes to presentation. Polishing machines are essential for achieving a high shine and for smoothing out any tool marks left from the preceding fabrication processes. These machines can range from simple handheld devices to more complex rotary tools used in professional studios.
When considering a polishing machine, it's crucial to think about:
- Speed Control: Too much speed can cause overheating, which negatively affects the metal.
- Bowl Size: Larger bowls can accommodate bigger items but may take up more workspace.
- Buffing Wheels: Different types of wheels serve various purposes, from satin finishing to high gloss polishing.
The right polishing machine not only improves the quality of the surface finish but also saves time, allowing jewelers to focus on design innovation rather than tedious finishing work.
Bead and Gemstone Setting Tools
Setting stones can be a daunting task, especially when aiming for perfection. Intermediate setting tools are invaluable for both new and intermediate jewelry makers. There’s a balance to strike, as proper tools can greatly affect the security and aesthetics of the final product.
Among the essential tools for stone setting are:
- Bezel Settings: Used for securing gemstones within a metal frame.
- Tweezer Tools: Specialized tweezers help in placing and manipulating small stones without damaging them.
- Prong Pusher: This is a go-to tool for setting stones securely in pronged settings.
Incorporating these tools allows jewelers to achieve more professional results, giving their work an edge. Allowing stones to take center stage is often what sets a good piece apart from a breathtaking one.
"Investing in quality intermediate tools not only bridges gaps in craftsmanship but also opens new avenues for creativity and expression in jewelry design."
These intermediate equipment choices are more than mere tools; they embody the skills and artistry that elevate simple metal and stone into beautiful works of art. By mastering them, jewelers can refine their expertise and bring unique visions to life.
Advanced Ring Making Equipment
As one delves further into the intricate world of ring making, the importance of advanced equipment cannot be understated. For both professional jewelers and dedicated hobbyists, these tools serve as a bridge between basic craftsmanship and extraordinary artistry. They not only amplify creativity but also enhance precision, efficiency, and the overall quality of the final product. By investing in advanced ring making equipment, artisans can explore new designs, streamline production, and ultimately push the boundaries of what's possible in jewelry making.
Laser Cutting Machines
Laser cutting machines are revolutionizing the way jewelers approach design and fabrication. This technology uses focused laser beams to cut through various materials with astonishing accuracy. Below are several critical benefits of incorporating laser cutting into the ring-making process:
- Precision: A laser cutter can execute intricate patterns and designs that would be nearly impossible to replicate by hand, down to a fraction of a millimeter.
- Speed: These machines perform cuts faster than traditional methods. This efficiency allows jewelers to produce more designs in less time.
- Versatility: Lasers can work on a range of materials, including metals and gemstones, opening up new creative avenues.
However, it's important to consider factors like the initial costs of these machines and the need for training to operate them effectively. By keeping up with technological advances, jewelers can maintain a competitive edge in an ever-evolving market.
Computer Numerical Control (CNC) Machines
CNC machines represent another leap forward in ring making, allowing jewelers to automate design processes with precision. These machines interpret digital files and transform them into three-dimensional creations. The advantages of CNC technology are noteworthy:
- Customization: CNC allows for high levels of customization in designs, accommodating specific tastes or unique client requests.
- Reproducibility: Once a design is programmed, it can be reproduced with consistency, ensuring every piece matches the original specifications.
- Reduced Labor: By minimizing manual labor, CNC machines free up time for artists to focus on the creative aspects of jewelry design.
Despite these benefits, jewelers must be aware of the learning curve associated with CNC programming and the ongoing maintenance that these machines may require to stay at peak performance.
3D Printing Technology
3D printing technology has also carved its niche in the realm of advanced ring making. It allows for rapid prototyping and the ability to test designs before committing to final materials. Here’s why integrating 3D printing into jewelry making is advantageous:
- Rapid Prototyping: Jewelers can create quick samples of their designs, making it easier to adjust and finalize concepts before production.
- Complexity: This technology permits the creation of complex and elaborate designs that traditional methods may struggle to produce.
- Material Usage: 3D printing can reduce waste, as it generally uses only the material required for each piece, promoting a more sustainable approach to jewelry making.
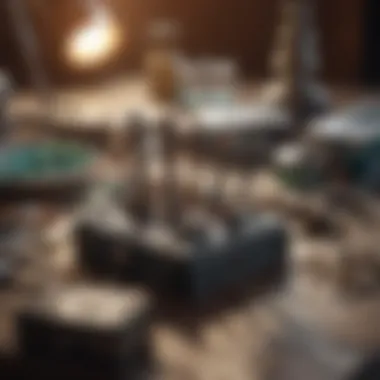
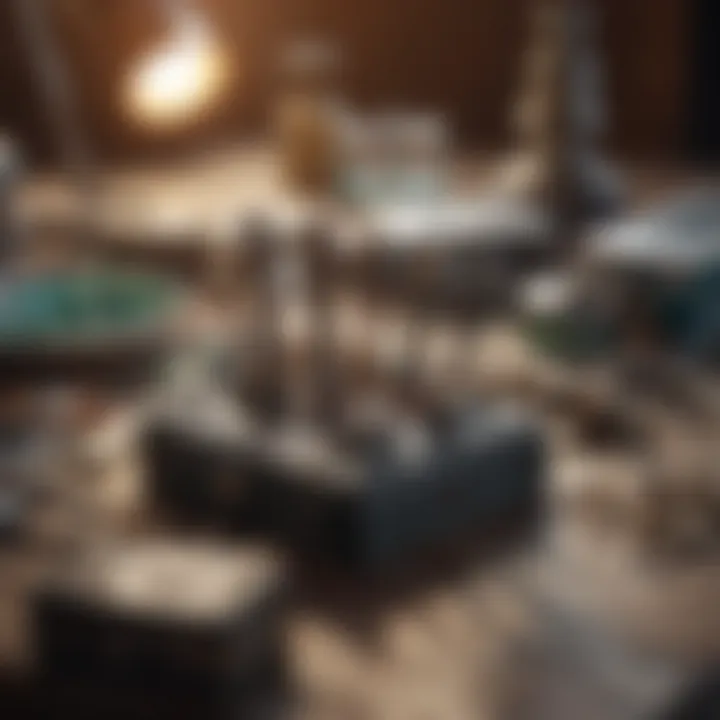
Nonetheless, the quality of the finished product can vary greatly depending on the printer used, so it's vital to select quality machines and materials to ensure a professional result.
Material Considerations
Selecting the right materials plays a crucial role in the art of ring making. From the fundamental properties of metal types to the ethics behind sourcing gemstones, understanding material considerations will significantly influence not only the durability and aesthetic appeal of the jewelry but also align with the growing trend towards sustainability in the jewelry industry.
Metal Types and Their Properties
When it comes to metals, jewelers face an array of options, each with distinct characteristics. Silver, for instance, is highly favorable due to its malleability and beautiful sheen. Many choose sterling silver for its strength, though it does tarnish over time.
Gold, often seen as the gold standard (pun intended), comes in various karats. The higher the karat, the purer the gold. But be aware, it can be softer and more prone to scratching. Platinum, on the other hand, is dense, durable, and resists tarnishing, making it a premium choice for high-value pieces – and often, it commands a higher price.
- Common Metal Types:
- Sterling Silver
- Yellow Gold
- White Gold
- Rose Gold
- Platinum
You may also want to think about alloys, which combine different metals to bolster strength and modify color. For instance, a little copper might be mixed to create red hues in rose gold. Understanding these properties helps jewelers make informed decisions when crafting rings.
Choosing the Right Gemstone
Picking the right gemstone is not a mere aesthetic choice; it’s a reflection of the customer’s personality and the message they want to convey. Each stone carries different meanings and associations, so it’s important to consider both appearance and symbolism.
For instance, diamonds are often given as symbols of love and commitment, while sapphires might appeal to those favoring loyalty and wisdom. Emeralds, with their lush green tones, can represent renewal, making them popular for spring-themed jewelry.
Before you start setting a stone, think about:
- Durability: Consider hardness on the Mohs scale. Diamonds score a 10, making them the hardest.
- Color: Does the hue resonate with the design intent?
- Clarity: How clear is the gemstone? Flaws can affect desirability.
"The right gemstone can transform a simple ring into a meaningful artwork."
Sustainability in Material Sourcing
In today’s world, where consciousness about our planet is rising, sustainability cannot be overlooked. This principle should guide every ring maker when selecting materials. Sourcing responsibly not only protects the environment but also promotes ethical practices within the jewelry industry.
Several considerations must be addressed:
- Ethically Sourced Metals: Ensure your suppliers adhere to fair trade practices. Look for certifications that guarantee materials are sourced responsibly.
- Recycled Materials: More jewelers are opting for recycled metals and reusing gemstones. Not only does this reduce waste, but it also supports a circular economy.
- Eco-Friendly Stones: Alternatives such as lab-created diamonds or colored sapphires offer an eco-friendly option, eliminating the need for mining and its associated environmental damage.
As a designer or hobbyist, integrating sustainable practices into your work not only enhances its social value but also resonates with eco-conscious consumers.
Safety Measures and Best Practices
In the realm of ring making, safety measures and best practices are fundamental. Engaging in jewelry crafting involves a range of tools and materials that can present risks. Therefore, understanding these safety protocols not only protects the artisan but also enhances the overall experience while working. From sharp instruments to hot equipment, the right safety gear and organizational practices can safeguard against potential mishaps, allowing jewelers to focus on their creative projects with peace of mind.
Protective Gear
Every ring maker should regard protective gear as a must-have, akin to a fisherman never leaving shore without a life jacket. This gear plays a crucial role in preventing injuries while handling tools. Basic protective equipment includes:
- Safety Glasses: Shielding the eyes from flying debris is vital, especially when cutting or soldering. A moment of distraction could lead to an eye injury.
- Gloves: When working with metals, gloves designed for jewelry making can shield against cuts and scrapes. However, care must be taken with certain tools where gloves may pose a snag risk.
- Aprons: A sturdy apron not only guards against metal specks but also keeps clothing clean and free from potentially hazardous materials.
Investing in quality protective gear may seem like an extra expense, but it saves from costly injuries and discomfort down the line, allowing for a focused and safer working environment.
Workspace Organization
A well-organized workspace goes hand in hand with safety. Without order, tools can easily become mislaid, increasing the risk of accidents. Here are some key considerations:
- Designated Tool Storage: Assign each tool a specific place and return it there after use. This habit minimizes the chance of forgetting where a cutter is or leaving a soldering torch unattended.
- Clear Work Surface: Maintain a clutter-free space to provide ample room to maneuver tools and materials. Any stray items can become tripping hazards.
- Proper Lighting: Good lighting is necessary to see detailing work accurately. Dim areas can lead to miscalculations and potential injuries while handling small parts.
An organized workspace doesn’t just enhance safety—it also boosts productivity. It’s easier to think clearly when the environment is tidy and everything is within reach.
Emergency Protocols
No one likes to think about emergencies, yet being prepared can mean the difference between a minor scare and a serious incident. Here are several recommended steps:
- First Aid Kit: Keep a well-stocked kit nearby and ensure all who work in the space know its location. Regularly check the contents to ensure everything is up-to-date.
- Fire Safety: Since soldering can lead to fire risk, ensure there’s a fire extinguisher nearby, particularly one suitable for electrical and metal fires. Knowing how to use it can save lives and property.
- Emergency Contacts: Compile a list of emergency contacts that can be reached quickly. This should include local medical facilities, poison control, and any personal contacts who can assist in case of an incident.
Implementing effective emergency protocols might seem tedious, but it protects not just the individuals working but also the creative space itself. Being prepared arms you against chaos and fosters confidence.
In the world of jewelry making, safety isn't just a regulation; it's a commitment to a healthy working environment and efficient craftsmanship.
Innovations in Ring Making Equipment
The landscape of ring making has changed dramatically over the last few years. As technology progresses, so does the range of tools available to jewelry makers, enabling them to create pieces that were once deemed too complex or simply impossible. Innovations in ring making equipment not only enhance the precision and efficiency of the crafting process but also provide jewelers with fresh avenues for creativity. With the ever-evolving demands of the market, understanding these innovations is essential for both hobbyists and professionals.
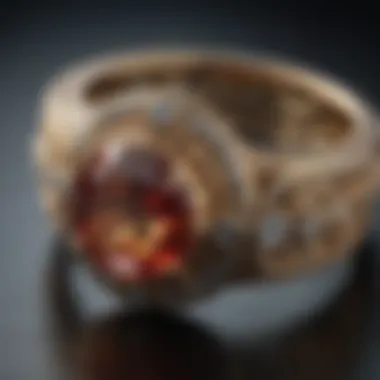
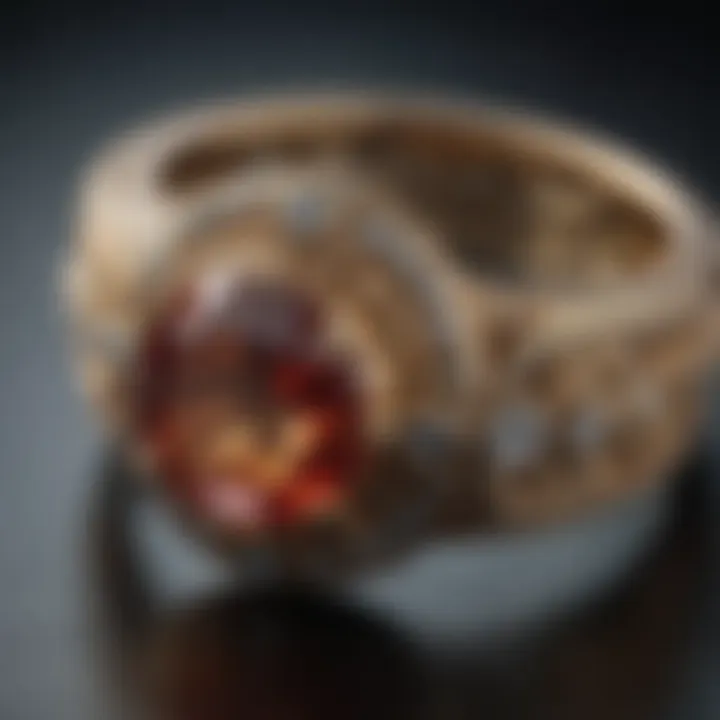
Emerging Technologies
Emerging technologies play a vital role in shaping how rings are designed and produced today. One cannot underestimate the impact of advancements such as laser cutting, 3D printing, and CNC machining. Each of these technologies has revolutionized the way jewelers approach their craft.
Laser Cutting
Laser cutting provides unmatched precision. Instead of traditional materials being cut using manual tools, lasers allow for intricate designs to be cut swiftly and accurately. This method minimizes waste by ensuring a clean cut, whereas manual techniques often result in excess material being removed.
3D Printing
On the other hand, 3D printing has made the prototyping process a breeze. Jewelers can quickly print a model of their design, assess its form, and make adjustments before committing to the final piece. This not only saves time but also allows for experimental designs without the fear of financial loss. The ability to use different materials in 3D printing adds an extra layer of flexibility to the creative process.
Digital Design Software
The advent of digital design software has completely changed the way jewelry is conceptualized. Programs like RhinoGold and MatrixGold integrate CAD technology to facilitate detailed modeling of rings. This software allows jewelers to visualize their designs in real-time, making minute adjustments with ease.
- Precision: Designs can be scaled and modified without any loss of detail.
- Client Collaboration: Digital models can be shared with clients for feedback, improving client satisfaction and ensuring that their vision aligns with the final product.
- Inventory Management: Digital records allow artists to maintain inventories of their designs, streamlining the production process and reducing errors.
"As technology continues to evolve, jewelers must adapt or risk falling behind in an increasingly competitive market."
With the right tools and awareness of advancements, jewel makers can enhance their artistry while maintaining the personal touch that defines handcrafted jewelry. The integration of emerging technologies and digital design software is undoubtedly paving the way for a new era in ring making, one that balances time-honored traditions with the efficiencies of modern practices.
Maintaining and Caring for Equipment
Taking proper care of ring making equipment is not just about keeping tools clean and shiny; it has far-reaching implications for both the quality of craft and the longevity of the tools themselves. As any seasoned jeweler will tell you, consistent maintenance can save money in the long run and elevate the overall standard of one's work. Well-kept tools yield better results, and that’s an undeniable fact. When tools function optimally, there is less room for mistakes. Less clutter and more efficiency in workspace organization lead to smoother production processes, fostering creativity and innovation.
Moreover, regular maintenance routines can help in identifying wear and tear before they lead to significant issues. Whether you’re a hobbyist or a professional, investing time in understanding how to maintain your tools is crucial. From cleaning to calibration, let’s delve deeper into what this entails.
Regular Maintenance Routines
To ensure that each piece of equipment performs at its best, consider establishing a maintenance routine. It may sound tedious, but like any good habit, it pays off in spades. Here are some key elements to incorporate into your regular maintenance:
- Cleaning: After every use, ensure you wipe down tools to remove dust, oils, or debris. For tougher stains, a gentle jewelry cleaner can work wonders. It’s important to follow up this step with a thorough drying to avoid corrosion, especially on metal tools.
- Lubrication: For moving parts, usage of a machine oil ensures smooth operation and minimizes friction, which can lead to unnecessary wear.
- Calibration: This is particularly relevant for precision equipment such as laser cutters and CNC machines. Regularly check settings to ensure accuracy.
- Inspection: Record any signs of damage or wear. If you notice fraying wires or rust, it might be time to replace that component.
- Storage: When not in use, store your equipment in a dry, dedicated area away from direct sunlight. Utilize toolboxes or padded cases.
By consistently applying these practices, you'll elongate the lifespan of everything in your workshop.
Troubleshooting Common Issues
Every jeweler, regardless of skill level, will face challenges as they work through the ring-making process. Recognizing and addressing these issues is essential to maintaining efficiency and preserving the quality of your creations. Below are some common problems, along with suggestions for troubleshooting:
- Sticking Tools: If pliers or cutters are not opening or closing smoothly, it may indicate dirt buildup. A simple cleaning with soapy water followed by proper drying might do the trick. In stubborn cases, a small drop of oil can help.
- Precision Errors: If your measurements seem off, first check to see if your tools are calibrated. Always revisit the instruction manual for calibration details. If the equipment appears damaged, consulting a technician may be necessary.
- Heating Issues: If soldering equipment isn’t reaching the desired temperature, inspect for faulty connections. Sometimes, a simple change of the gas can remedy the problem.
- Marking or Damage on Materials: If gems or metals show scratches post-processing, consider the tools used for the job; rough edges may need smoothing.
Remember, proactive problem-solving is key to good craftsmanship. Staying vigilant can keep minor glitches from developing into costly repairs.
In sum, maintaining and caring for ring-making equipment is as essential as the crafting process itself. Establishing solid maintenance routines and troubleshooting common issues can lead to fruitful outcomes in jewelry making, setting the stage for creativity and excellence. By adhering to these principles, jewelers can ensure that their passion translates into quality craftsmanship, whether they're crafting forever rings or intricate designs.
The Future of Ring Making Technology
The world of ring making is on the cusp of revolutionary advancements. The integration of technology is not just altering how rings are made but also expanding the possibilities of creativity and precision. Understanding the future of ring making technology plays a pivotal role in keeping jewelry artisans ahead in this competitive field. From trends shaping production to evolving consumer tastes, the landscape is shifting rapidly.
Trends in Jewelry Production
One of the most notable trends in jewelry production is the rise of sustainable practices. As environmental consciousness grows among consumers, jewelers are turning their attention to eco-friendly materials and processes. For instance, vintage metals and ethically sourced gemstones are gaining prominence. Many brands are now committed to using recycled materials, which helps in reducing waste and promoting overall sustainability.
"This shift towards sustainability is not merely a passing fad; it represents a profound change in consumer expectations and industry standards."
Another trend is the increasing use of digital manufacturing techniques. Technologies like 3D printing and CNC machining are making it more feasible for artisans to produce intricate designs with precision. Such methods allow for rapid prototyping, which means jewelers can experiment with designs and turnaround times have significantly improved. Additionally, these technologies minimize material waste, aligning with the growing eco-conscious sentiment.
Consumer Preferences and Customization
As consumers become more discerning, their preferences continue to shift towards personalized solutions. The demand for custom jewelry is on the rise, with individuals eager to express their unique stories through their accessories. This growing preference is pushing designers to leverage technology for customization. Engaging with customers digitally—through interactive design tools, for instance—enables jewelry makers to tailor their creations finely.
The shift toward online shopping coupled with augmented reality (AR) tools is transforming how consumers experience ring shopping. Tools developed by brands now allow potential buyers to visualize how a ring would look on their finger, adding a new layer to the buying experience. Moreover, this trend requires jewelers to invest in quality digital platforms that can support such technologies along with secure transactions.
In summary, the future of ring making technology hinges on innovations in sustainability and personalization. It's not just about adapting to trends but also about anticipating them. Jewelers prepared to embrace these changes will find themselves better equipped to meet the needs of a growing, quality-focused market.
End
Bringing this journey through the various tools and equipment for ring making to a close, it is essential to reflect on the significance of understanding these elements. From the basic tools that a novice would rely on to the sophisticated technology utilized by seasoned professionals, each piece of equipment holds its own value in the intricate process of jewelry crafting. This article illustrates how both traditional and modern techniques play a role in shaping the art of ring making and enhancing the jeweler's creativity.
In focusing on the practical aspects of each tool, readers gain insights into their unique functions and advantages. Such knowledge not only serves as a foundation for newcomers eager to embark on their jewelry-making journey but also as a resource for experienced artisans looking to refine their craft. Considering aspects like safety measures, material selection, and maintenance routines, it’s clear these elements are not just trivial details—they're vital components in creating stunning pieces of art that stand the test of time.
Summary of Key Points
- Understanding Equipment: Recognizing the functions of each tool aids in mastering the craft.
- Historical Relevance: Learning about the evolution of ring-making tools provides context and inspiration.
- Material Choices: Selecting the right metals and gemstones can enhance the aesthetic value and durability of the jewelry.
- Safety Protocols: Implementing proper safety measures is crucial in maintaining a safe workspace, ensuring the jeweler's well-being.
- Maintenance: Regular upkeep of equipment ensures longevity and optimal performance throughout the crafting process.
Final Thoughts on Ring Making Equipment
As we step forward into the future of jewelry making, the array of tools available continues to expand, reflecting advancements in technology and shifts in consumer preferences. Embracing innovation while acknowledging the artistry of traditional methods creates a well-rounded approach to ring crafting. The convergence of creativity, precision, and engineering heralds a new era for jewelers.
While the essence of ring making remains rooted in skilled craftsmanship, the tools one chooses play an instrumental role. Perhaps the most significant takeaway is this: no matter the level of expertise, understanding and respecting the value of each tool—and how they interact within the craft—can lead to extraordinary results. Whether you are a budding artisan or a seasoned jewelry designer, the tools at your disposal are not merely instruments; they are bridges to your artistic vision.